Table of Contents
Introduction
In the highly competitive manufacturing landscape, production efficiency is the key to a company’s success. One area where significant improvements can be made is in the liquid – filling process. Double head rotor pump filling machines have emerged as a game – changer, offering a multitude of ways to enhance production efficiency. This article will explore how these machines work and the specific ways they contribute to a more productive manufacturing environment.
Understanding Double Head Rotor Pump Filling Machines
A double head rotor pump filling machine is a specialized piece of equipment designed to fill containers with liquids. The term “double head” indicates that the machine is equipped with two filling heads, which operate simultaneously. The heart of the machine is the rotor pump, a positive – displacement pump.
The rotor pump consists of rotors that rotate within a housing. As the rotors turn, they create chambers that trap and move the liquid from the inlet to the outlet. This mechanism ensures a consistent and controlled flow of liquid, which is essential for accurate filling.
Ways Double Head Rotor Pump Filling Machines Boost Production Efficiency
High – Speed Filling
The most obvious way these machines enhance efficiency is through their high – speed filling capability. With two filling heads working side by side, the machine can fill two containers at the same time. This effectively doubles the filling rate compared to a single – head machine.
For example, in a beverage bottling plant, a single – head machine might be able to fill 50 bottles per minute. A double head rotor pump filling machine, on the other hand, can fill 100 bottles in the same amount of time. This significant increase in throughput allows manufacturers to meet larger production demands in less time, reducing the overall production cycle.
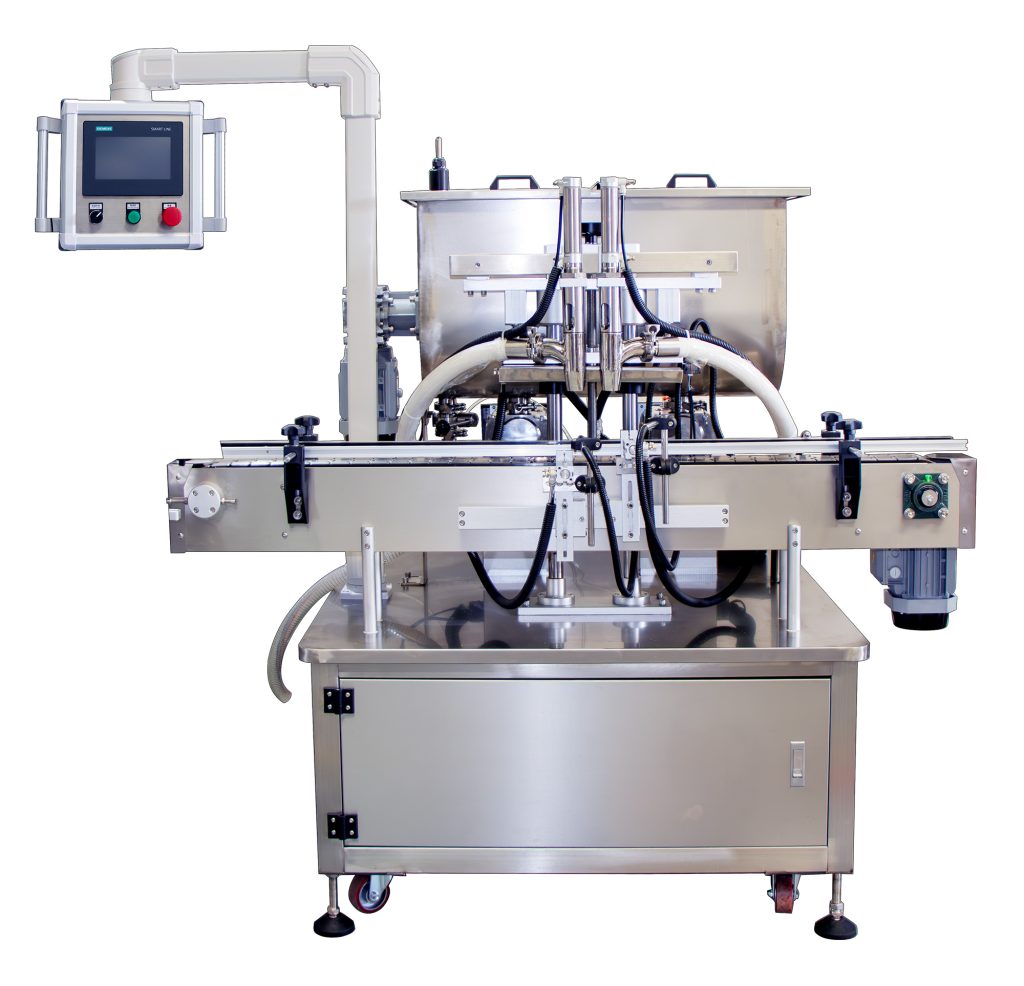
Precise Volume Control
Accurate filling is crucial for maintaining product quality and reducing waste. Double head rotor pump filling machines offer precise volume control. The positive – displacement nature of the rotor pump ensures that the same amount of liquid is dispensed into each container with high accuracy.
In the pharmaceutical industry, where precise dosing is a matter of life and death, these machines are invaluable. They can fill medications into vials or syringes with extremely small tolerances, ensuring that each dose is consistent. This precision also reduces the amount of product that is over – filled or under – filled, which would otherwise be wasted.
Reduced Downtime
Downtime is a major enemy of production efficiency. Double head rotor pump filling machines are designed to be reliable and require minimal maintenance. The simple and robust design of the rotor pump means fewer moving parts that can break down.
Additionally, these machines are often equipped with self – cleaning and self – diagnostic features. The self – cleaning function helps to prevent clogging and contamination, which can cause production stoppages. The self – diagnostic system can detect potential problems early, allowing operators to address them before they lead to significant downtime.
Compatibility with Different Liquids and Containers
Double head rotor pump filling machines are highly versatile. They can handle a wide range of liquids, from thin, watery substances to thick, viscous materials like pastes and gels. This versatility means that a single machine can be used for multiple products within a manufacturing facility.
Moreover, these machines can accommodate different container sizes and shapes. Whether it’s small vials, large bottles, or irregularly shaped containers, the double head rotor pump filling machine can be adjusted to fill them accurately. This eliminates the need for multiple filling machines for different products and containers, saving both space and money.
Easy Integration with Production Lines
To maximize production efficiency, it’s important that all equipment in a production line works together seamlessly. Double head rotor pump filling machines are designed for easy integration with other production equipment such as conveyors, cappers, and labelers.
The machine can be synchronized with the conveyor system to ensure a continuous flow of containers. It can also communicate with other equipment in the line, allowing for coordinated operation. For example, when a container is filled, the machine can signal the capper to start the next step in the process. This integration reduces bottlenecks and ensures a smooth and efficient production flow.
Conclusion
Double head rotor pump filling machines offer a comprehensive solution for boosting production efficiency. Their high – speed filling, precise volume control, reduced downtime, versatility, and easy integration make them an essential piece of equipment in modern manufacturing. By investing in these machines, companies can increase their productivity, improve product quality, and gain a competitive edge in the market.